Sunday, July 02, 2006
Norheimsund, June 29
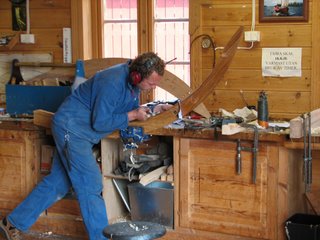


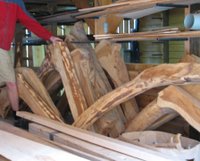
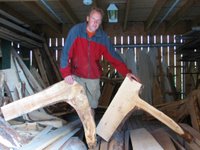
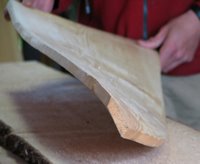
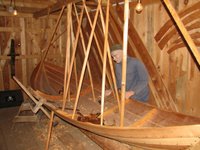

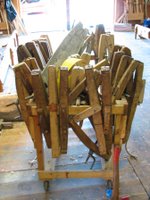
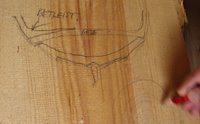
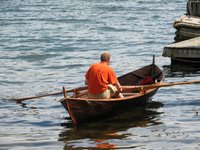
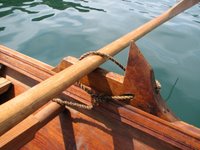
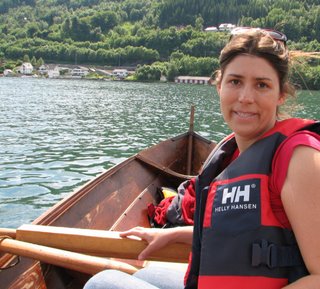
Norheimsund is a small town on Hardangerfjord, one of the fjords near Bergen. The Hardanger Fartøyvern Senter is a boatbuilding workshop where boats are built and restored in a very traditional way. The boats being made here now are traditional types of fishing boats that have been made in this harbor for hundreds of years.
I went straight from the bus to the center at 9am, where all of the employees were having breakfast together. They had been working since 7am. Anders Geertsen, one of the boatbuilders, was expecting me. He is a friend of a friend of a friend of a friend . . . this is how a lot of my trip is possible! Anders began to show me around. He had just finished a boat that week, so on this morning he was starting a pair of boats. He was working on making the stern pieces, the ends of the keel. These have a special shape where they are notched to let in the top strake.
Anders was working fast, so he let Peter Helland-Hansen, his boss, show me around and give me the crash course in building færving, the four oar fishing boats being produced here. Peter explained that these boats needed to be strong, and in boatbuilding, strength is very much a function of flexibility. Most of boatbuilding construction has evolved over time to produce a strong and flexible boat. Many of the bent parts in the boat are from grown curves in wood, pieces of wood that are naturally bent in the curve or angle needed. Using grown curves is not only a simpler and more efficient technique for getting a curved piece of wood, but it is also more flexible than joining together an angle from 2 pieces, and probably also more flexible than a bent laminated curve.
The ribs in the stern and the bow of the boat are the rongs, and these are shaped from large pine tree roots that already have a 90 degree angle in them. Up until the 1890's, the type of færving now called the Hardanger boat was built with the gunnels at the top edge of the boat stopping at the rongs and not continuing all the way up the bow or the stern. This added to the flexibility of the boat, and made it just that much lighter weight. When a fisherman would buy a boat, he would grab hold of the stern and shake the boat, judging the flexibility of the boat by how much it wiggled. That was a good thing in the waves.
After 1900, the type of færving called a strandebarmer was being built. In this one, the gunnels did go all the way up the bow and stern. This was probably not at the request of the fishermen. This was likely a result of a boom in boatbuilding at that time that led to an influx of boatbuilders from eastern norway. These boats are stiffer, which would have been fine for use as pleasure boats and rowboats for summer homes on the fjords. The fishermen continued to order boats in the older style.
Once the keel is built (that's the long rib down the entire length of the bottom of the boat), the first boards, or strakes, are attached. The bottom strakes are the most shaped. Their shape is a compound curve that is both twisted and has a concave hollow. The shape of the bottom strake, or the hals, is critical for quickly cutting into the water, and then pushing the water up and under the boat. A good shape on the bottom of the boat meant easier rowing for the fishermen. The halsar are cut from a split log. First one would cut the plan view of the hals from the half log. Then the surface of the twisted shape is hewn with an axe. Next, an even thickness plank is sawn with a 2-man handsaw to make a parallel cut to the twisted surface. This shaped and sawn twisted board must be extra thick, about 2 inches, because there is still more shaping to do. Finally, the twisted board is scooped out with and axe and a coopering plane in order to get the concave curve. It is pretty simple equipment being used to make these boats, mainly hammers, saws, axes, and planes. The shapes are very complex, but they are made almost entirely without drawings.
Once the shaped halsar are connected to the keel, the rest of the strakes (usually 2 more on each side) are pulled into place and nailed together. The top strakes are not shaped the way the halsar are. They are sawn. The way they are pulled into place is by holding the planks down with sticks wedged between the plank and the low beam of the workshop, and then clamping them with these excellent clamps that I need to make when I get home. They are like pinchers. They have a whole rack of them at the workshop. The planks are then nailed with a nail and a square washer, and the nail is peened over on the inside. These are clinker build boats. The rongs (end ribs) and the other ribs in the middle of the boat ( the band, bete, and betleist combination) are put in after the lappstraking is complete. The boats are then painted with pine pitch to protect the wood.
The boat that had been finished earlier in the week had not been tested yet. Peter invited me to go for a row with him to make sure the boat was seaworthy. There really wasn't much doubt, but boats always need to have a go in the water before they are sold. This really made my day! I was already in woodworker heaven, but now I was going to get to row in Norway too.
It is a lot different from the way I row at home in an 8-man scull holding one oar. We each had 2 oars and sat on fixed benched. The oarlocks are square and the oars are very loosely held into place with a loop of rope. I felt pretty clumsy, but we managed to take the boat for a nice loop out from the harbor. Nice work if you can get it!
At the end of the workday, Anders and I went back to his house where I was staying. We looked at some amazing photos from his boatbuilding apprenticeship near Trondheim. He then had to go to the doctor to get a cut on his finger taped up, and then off to pick up his wife and baby. I walked up a trail on the hill to Peter's house, where I had dinner with Peter and his 2 youngest kids. His wife had taken the other two kids to a soccer camp. We made fish kebobs and looked at the sleds that Peter has made. Everyone in Norway has been so hospitable and kind. I hope I see Peter and Anders in California one of these days so I can return the favor.